8 Reasons Vertical Integration Matters
Encore Wire's 460 acre, single-site campus in McKinney, TX continues to grow. In 2023, we've expanded with the construction of our new, state-of-the-art, compounding facility. This addition affords us the ability to create cross-link polyethylene (XLPE) insulation along with other insulation compounding agents. The expansion combined with previous campus enhancements further deepens our vertically integrated business model.
As Encore Wire continues to broaden its capacity and capabilities, the performance and output are optimized. As a result, we're equipped to service customer needs better, faster, and more efficiently.
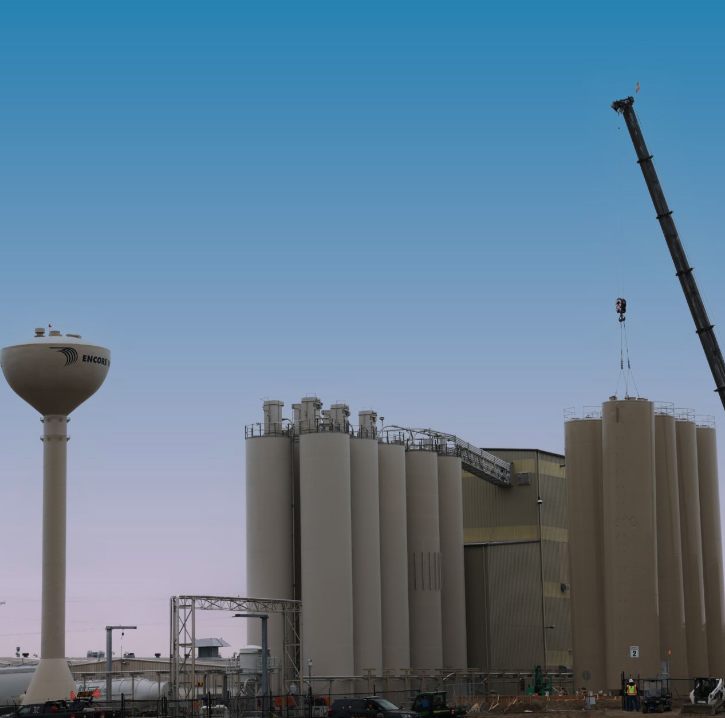
So why does having a vertically integrated manufacturer as your partner matter? Here are 8 reasons it can be a win-win for channel partners:
BENEFITS OF VERTICAL INTEGRATION
- Self-sustaining – With less reliance on external suppliers, waiting periods or down-time are virtually eliminated. Avoiding supply chain disruptions allows the manufacturer to continue business without missing a beat, so your project timelines stay on track.
- Operational agility – The ability to react and pivot at a centralized campus enables improved processes and greater efficiency - an advantage that allows the manufacturer to better serve customers' evolving needs.
- Speed to market – Steps including UL testing are done on site at Encore Wire's TechLab®. Rather than waiting on results from an off-site party, new products are introduced quickly to the market. Additionally, speediness in delivery of products (from a single-site campus, with one PO) creates a competitive advantage difficult to replicate.
- Costs are reduced – When producing material in-house, there's less reliance on the supply chain. This eliminates procurement and transportation steps in the process, which decreases overall costs and improves efficiencies. Savings can be applied toward reinvesting and better serving the customer base.
- Knowledge increases – With more steps completed on-site (versus relying on outside resources), there's a better overview of processes, and opportunities become more visible for continued development and improvement. Additionally, having the flexibility to react to market conditions and adapt to specific customer needs plays a key role where the benefit is passed on to the distributor, contractor, and end user.
- Positioned for high quality – Having direct control over raw materials used throughout the manufacturing process results in higher quality products. Logistics are simplified, and there are shorter turnaround times with fewer change overs needed. Vertical integration better positions the manufacturer in maintaining high standards while also allowing quick adaptability to react to marketplace changes.
- Marketability is improved – By taking ownership of more stages in the manufacturing process and in the selling of products and services with a vertical integration strategy, there's opportunity for higher brand awareness and loyalty among partners.
- Greater independence & control over process – With a self-sufficient business model, concerns for availability or unpredictable delivery from suppliers are virtually eliminated. There's resiliency and flexibility in the manufacturing process thanks to the independence created by a vertically integrated campus like Encore Wire's. The result equals more streamlined processes, high fill rates, quick turnaround times, and a focus on service excellence which is a win-win for everyone.
WHAT DOES THIS MEAN FOR YOU?
You can count on Encore Wire to deliver material when you need and how you need it. Having a reliable wire and cable manufacturing partner like Encore Wire takes the stress out of waiting or needing to adjust your project timelines.